Carrier Quadcopter
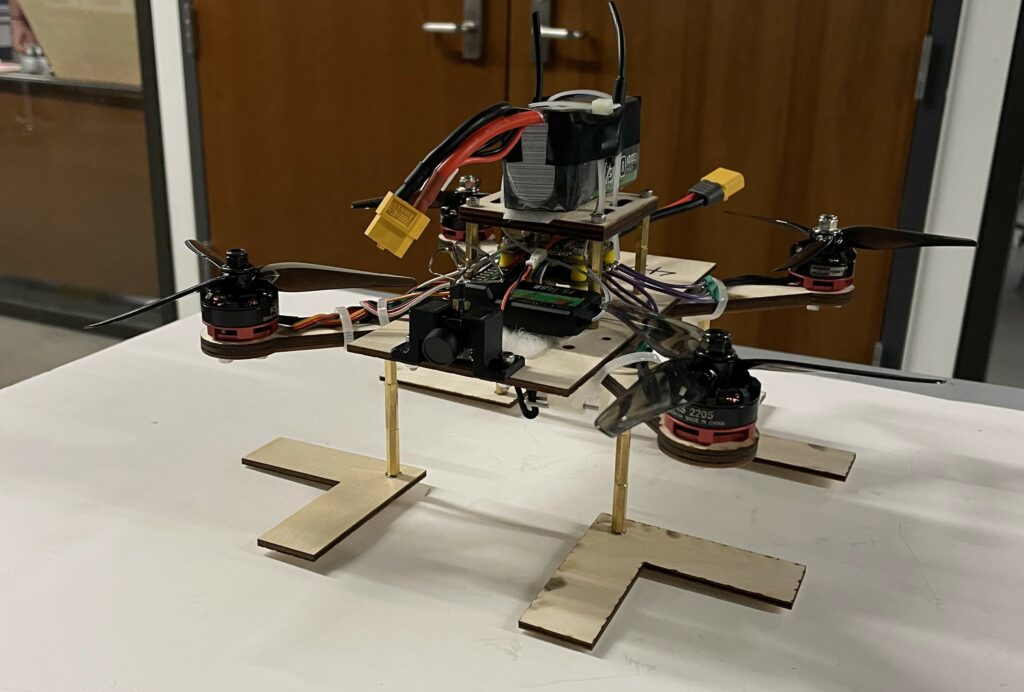
Objective: Design and fabricate a delivery drone to meet a local business requirement, adhering to a budget of $250.
For the final project in my design methodology course, our team partnered with the local CVS pharmacy to develop a drone delivery service for the university, leveraging its proximity and ability to access areas inaccessible by vehicles.
We employed the following electronics to achieve the core functionality of the drone.
Flight Controller: The selected FC, the SpeedyBee F405 V3 + ESC stack, provided a cost-effective solution with the essential functionalities needed for our drone. This flight controller also includes four integrated electronic speed controllers, enabling motor control.
Motors: We chose four Readytosky 2122 920 KV motors due to their 12V power input and thrust capibilities.
Radio Controller and Transmitter: The Flysky FS-i6X radio controller was selected due to its programmable buttons, which facilitate integration with our payload delivery system.
Camera: The WT03 Micro FPV AIO 600TVL Camera was chosen because it can be powered by the flight controller and allows the operator to view live feed on their phone.
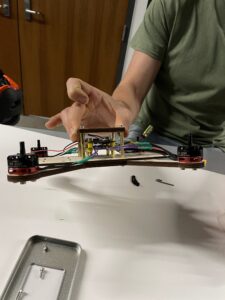
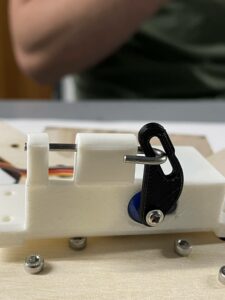
We implemented a pin release system for the delivery mechanism, featuring a rotating hobby servo that actuates a metal rod into a 3D-printed slot. Two brackets were designed: the first converts the servo’s rotational motion into horizontal motion of the pin, while the second secures the servo and pin system in place and guides the pin into the slot. Items for delivery are placed in a grocery bag held by the pin, which, upon reaching the drop-off location, is released by activating the servo to drop the payload.
The design process included a FMEA analysis to identify critical failure modes. Our manufacturing process followed the principles of Design for Assembly (DFA), Design for Environment (DFE), and Design for Manufacturing (DFM) to optimize our plan.
The final frame design featured a three-tier system to facilitate rapid maintenance in the event of a crash. The bottom tier housed the landing legs, payload delivery system, and motors. The second tier contained the flight controller stack, camera, and transmitter. The top tier was designated for the drone’s power source.
To minimize costs, 1/4″ plywood was selected for laser cutting the frame. Initially, 1/8″ plywood was considered, but finite element analysis (FEA) of the initial frame iteration indicated significant deflection under applied stress, leading to the material change.
For greater insight of the project, please take a look our final report.
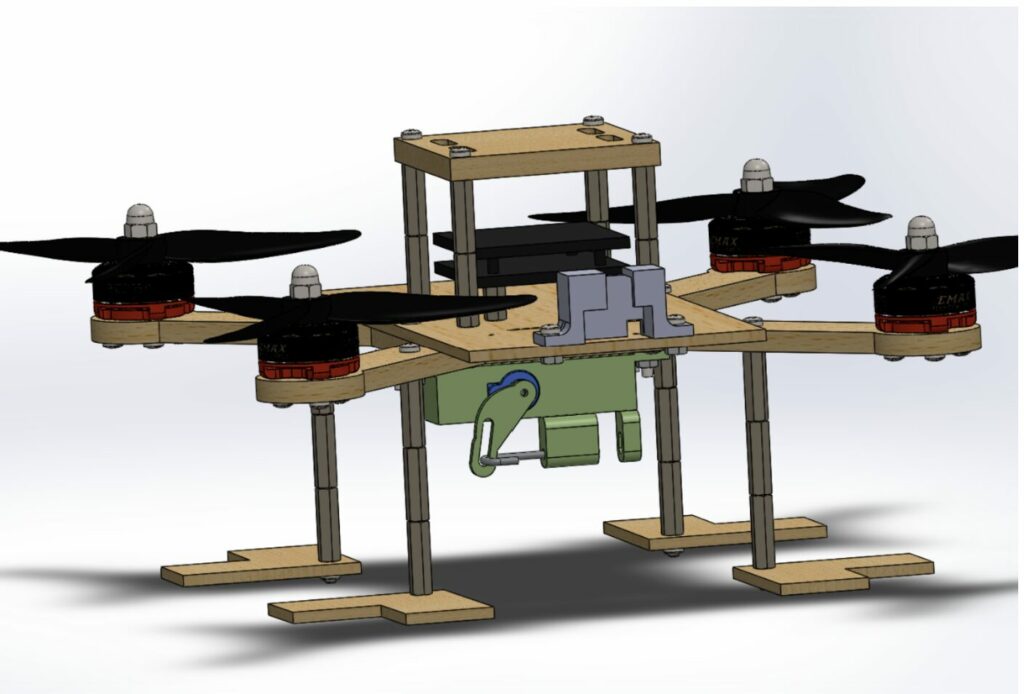
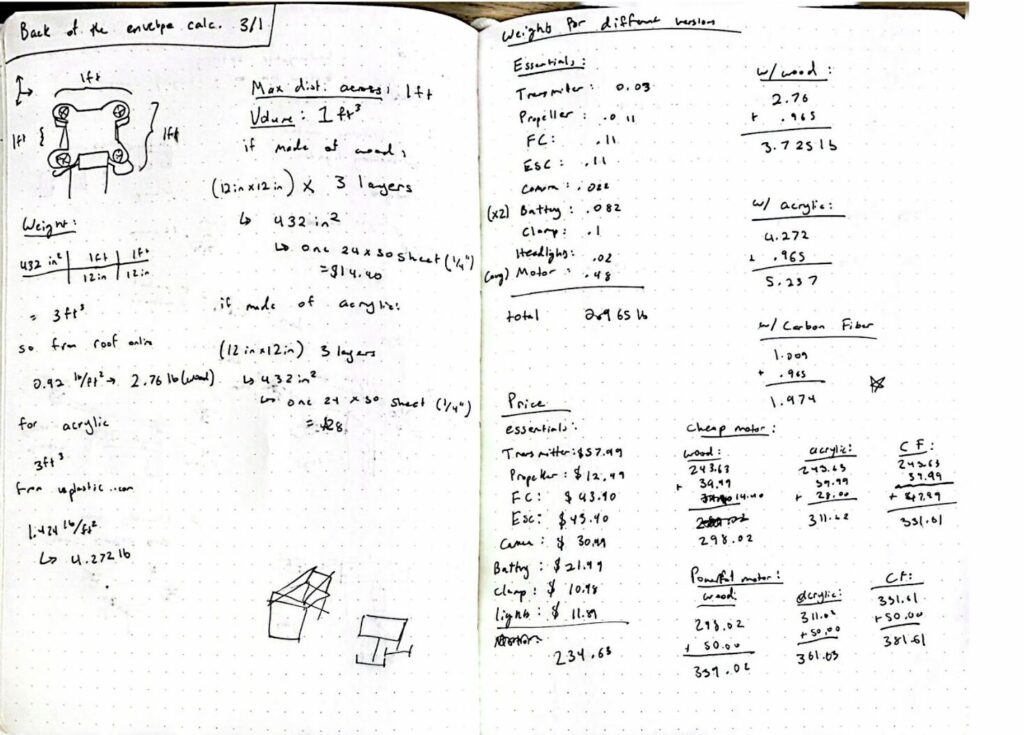
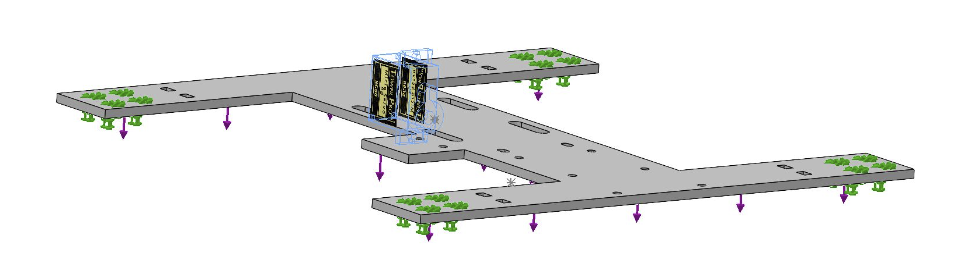
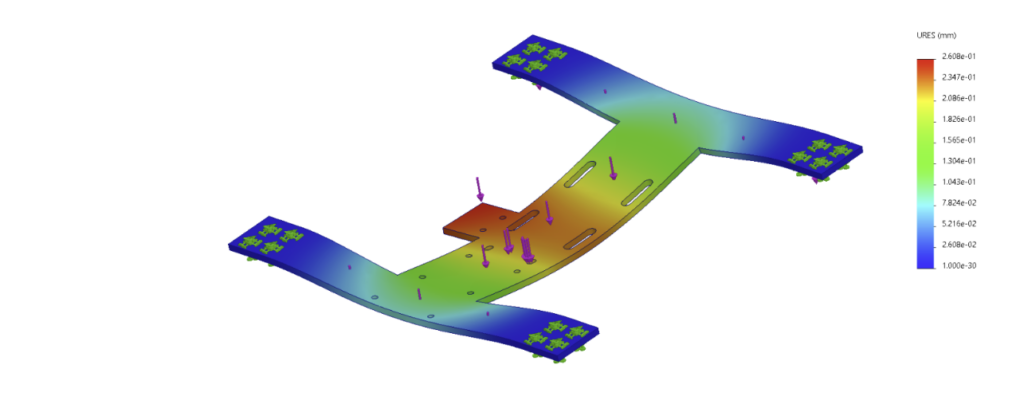
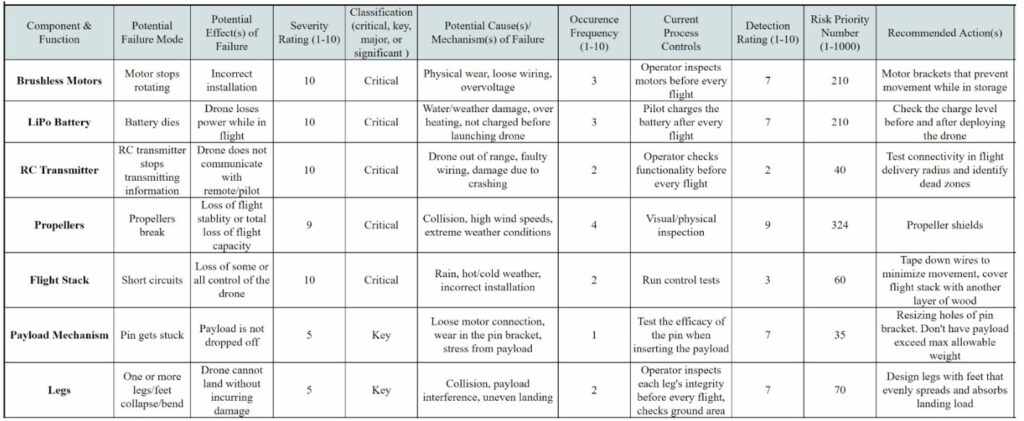